3D PRINTING: MAKES NEW COMPLEX SHAPES POSSIBLE
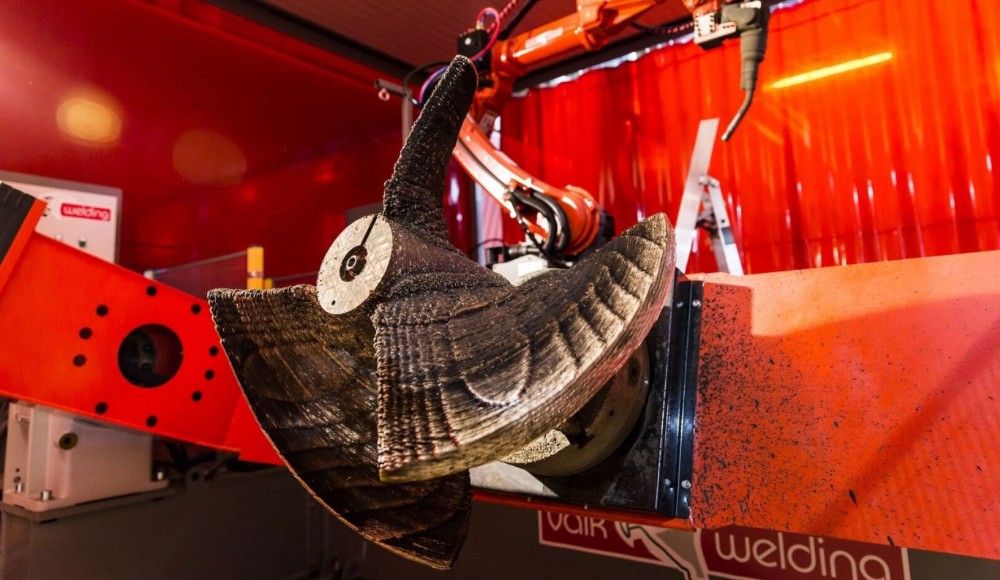
3D PRINTING IS DEVELOPING IN THE MARITIME SECTOR AT AN EXTREMELY FAST PACE, SAY GEERT SCHOUTEN AND CEES VERKERK OF MARINE SOFTWARE SPECIALISTS SHIPBUILDER
It’s hard to believe that it was little more than three years ago that Maersk Tankers began exploring the idea of 3D printing its own spare parts on board the vessel rather than transporting them to the ship. That first experiment took the (printed) form of a small plastic fan for an electric motor.
Flash forward to November 2017 and Damen Shipyards announced that a 3D-printed propeller had received class approval from Bureau Veritas. Designed by Promarin and created in partnership with the Port of Rotterdam’s Additive Manufacturing LAB (RAMLAB) with the support of Autodesk software and robotics expertise, the 1,350mm diameter WAAMpeller (WAAM - Wire Arc Additive Manufacturing) required 298 layers of Nickel Aluminium Bronze alloy.
The reason for rapid advance of 3D printing, or additive manufacturing (AM) as it’s otherwise known, is that companies are discovering its many advantages. Maritime companies can now print parts needed on site that would otherwise takes weeks to expensively source and then transport to a suitable location. In fact, we are now able to print parts that previously it would not have been possible to make at all which are lighter, more robust and more intricately shaped than their traditionally cast or moulded equivalents. Using CAD software it is possible to calculate the points of a component that will need to bear loads and halve the weight without compromising the structural integrity.
Current applications of 3D printing in maritime
One of the first maritime sectors to witness the impact of 3D printing has been superyacht construction, making it possible to realise the ever-more complex designs of the customer. Mullions, to give one example, now have even more sophisticated shapes then before the 3D printing era.
Another application of 3D printing is promoting the sustainability of the maritime sector and beyond. Take for example the thoughtful ‘one-minute-boat concept’ in which Shipbuilder participates. Devised by the Netherlands-based environmental consultancy Searious Business, the ‘one minute’ derives from the estimated 20 tonnes of plastic that are discharged into the world’s oceans every minute. The idea is that a yacht, with a nominal displacement value of 20 tonnes, will be 3D printed from recycled plastic waste that is collected worldwide from locations where it would othwerwise have ended up in rivers, seas and oceans. Without 3D printing this beautiful sustainable concept would never have gotten off the ground.
Class approval
As a proof of 3D printing’s growing maturity as a technology, it is now beginning to fulfil the requirements of maritime classification societies. In addition to the aforementioned BV certification, in November 2017 DNV-GL published its additive manufacturing class guidelines ‘DNVGL-CG-0197’ in order to assist in the certification process for materials and components and assure that parts created using AM have the same level of quality assurance as tratditionally manufactured products.
Trendsetters and students
We are beginning to see new maritime companies emerging that focus solely on 3D printing. Take for example one of the trendsetters in the maritime sector, Royal3D, a subsidiary of engineering company Royal Roos, which has entered into co-operation with 3D printer manufacturer CEAD BV to to print large, constructive ship components with a completely new 3D printing technology, called Continuous Fibre Additive Manufacturing (CFAM) on an industrial-size printer. This technology adds a continuous carbon or glass fibre to thermoplastic granulates (e.g polypropylene) while an internal heating mechanism prevents warpage or shrinkage during the printing and allows it to cool in a controlled manner. The end result adds considerable strength to the material. Royal3D also collaborates with students at Rotterdam Mainport University who will become the first to graduate with 3D printing as their principal maritime subject.
What are the current obstacles to further adoption?
Even though 3D printing is developing at an extremely fast pace, the technique still has its challenges. For example, the repeatability is small, which is not so much a handicap for 3D printing as an an additional consideration. It means that when it comes to larger components, identical parts aren’t printed in exactly the same way. In the maritime sector, these deviations per part are often considered to be too large.
It is one of the reasons we should not look for replacing existing manufacturing methods, but creating products with new shapes, combined functions, either one-off or with higher dimensional tolerance.
In addition, R & D teams from maritime companies are yet to get started! Currently too much work is aimed at simulating what is already there, using a 3D printer. Why? That is an end-of-line solution. We should be using this beautiful technique to print parts that otherwise could never have been made! Note that, to date, 3D printing is still more expensive than conventional manufacturing methods. That is why this technique should be deployed to make what has previously seemed impossible.
This is done in particular by looking differently at what a ship should look like and how much more ingenious we can now be. Just to think outside the box for a moment: consider the example of Taiwan-based artist Hung-Chih Peng, who last unveiled a 3D printed art installation, ‘The Deluge’, modelled after a shipwreck and made using 30 Desktop 3D printing 1,200 pounds of filament was made using 100,000 3D printed pieces and stands 26ft long.
On a more practical level there is the Airbus A320 nacelle hinge created by manufacturer EADS Innovation Works and Airbus Group Innovations-EOS as part of a ‘cradle to grave’ study into aerospace parts, processes and end-of-life strategies. Additive manufacturing and design-optimisation made it possible to significantly reduce the weight of the titanium bracket, adding up to a 40% reduction in CO2 emissions over its lifecycle and a weight reduction of 10kg per plane. What’s more, not only does the process only use the material actually needed, cutting titanium consumption by 25%, but total energy consumption for the initial raw metal powder is slightly less than conventional casting.
A typical current marine example is Sicilian boat builder Livrea’s project to build the world’s first 3d-printed racing yacht, with a hull made from multi-material polymer composites. The new design and manufacturing process cut production time from months to hours, while also reducing waste. Royal3D is taking the same design approach for bulkheads on cargo ships.
The future
In the next 10 to 20 years, 3D printing will be increasingly deployed for smarter construction of ships. The repeatability will continue to increase too. To achieve this, it is essential to focus maritime training on developing knowledge of 3D printing. After all, it is a completely new technique.
The business sector, such as the ever-innovative Royal3D, is setting a good example by involving students in this new technique. In Singapore there is a countrywide initiatives to develop knowledge of 3D printing, such as the recent Memorandum of Understanding (MoU) signed between Semcorp Marine, DNV GL, the A*Star Singapore Institute of Maritime Technology (SIMTech) and the National Additive Manufacturing Innovation Cluster (NAMIC) that aims to transform the country’s marine and offshore sectors. The agreement will look at fabrication of large-scale ship structures through 3D printing, as well as the use of drones for ship inspections and improving ship design and operations using digital twins.
Elsewhere, the University of New Brunswick’s Marine Additive Manufacturing Centre of Excellence has become the first in Canada to use 3D metal printing to manufacture certified parts for the industry. The centre’s stated mission is to ensure the adoption of AM in the Canadian industrial marine sector by developing methods, procedures, and effective workforce training systems. Among the areas it is focusing on are enhanced corrosion protection, hybrid printing, ‘smart parts’ and blast resistance.
Invest in the first steps!
But where do you begin with with 3D printing? IT experts can offer shipyards and naval architects workshops into the potential and possibilities of 3D printing. They will eventually help you plan the next step; working with an intelligent data management tool. From our experience we know input from experts is crucial when you start working with 3D printing. Shipbuilder has years of experience in guiding organisations when they start working with digital transformation.
For the original article visit: https://www.linkedin.com/feed/update/urn:li:activity:6379733960628465664
For the PDF visit: http://shipbuilder.nl/site/wp-content/uploads/2018/03/Naval-Architect-3D-printing.pdf